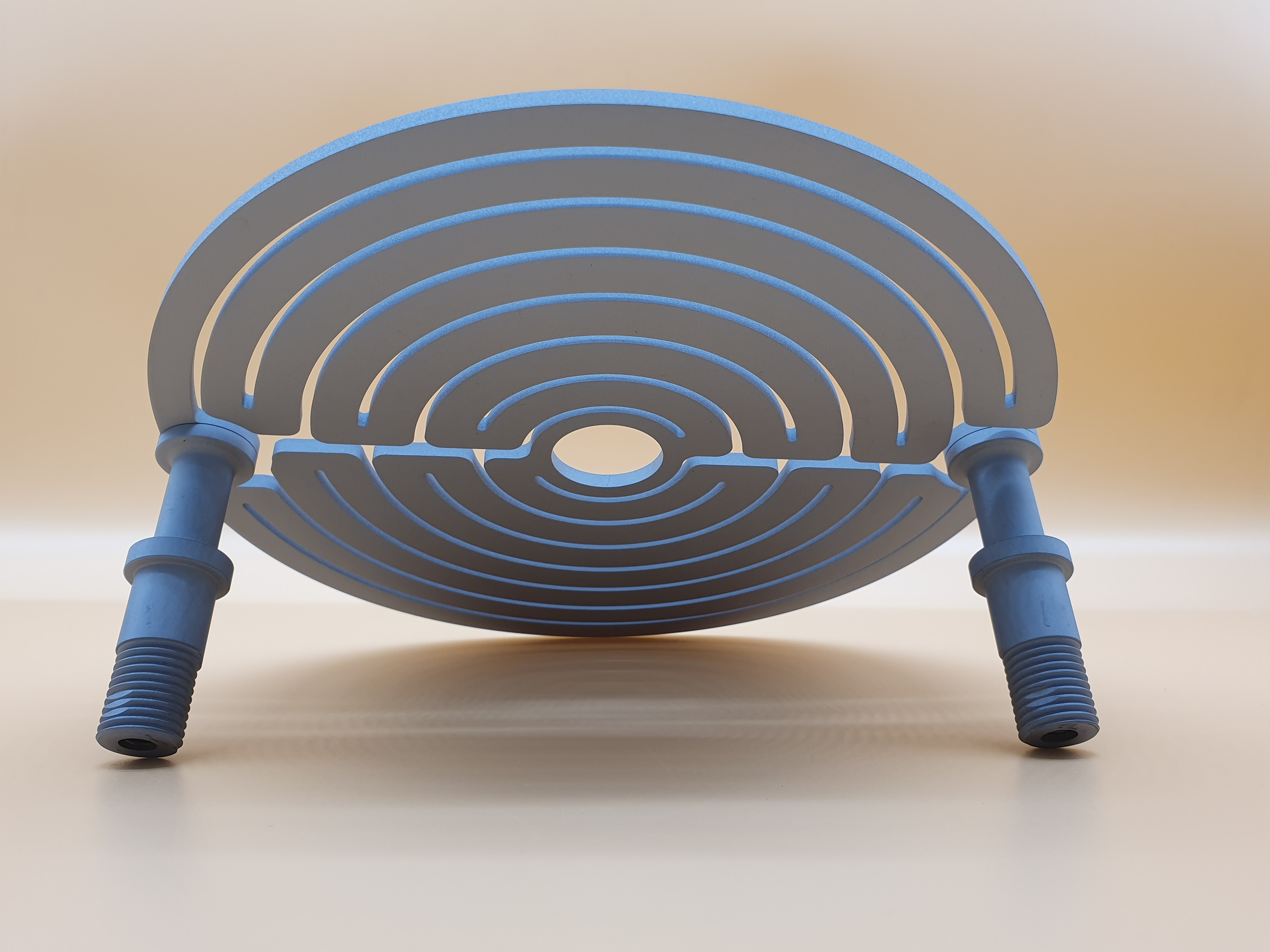
Silicon Carbide Coating (CVD)
The process is unique as it combines a well defined crystal size, isotropic structure and low surface roughness. The high growth rates achieved by SiC3 (Silicon Carbide cubed) ensures that the product remains cost effective.
The coating can be used in semiconductor, aerospace and heating technologies. It will provide a high purity and impervious layer on graphite, porous ceramics and composites. The combination of graphite selection and graphite machining expertise, offered by CGT Carbon, will ensure that customers experience optimal support for various critical components within these industries.
The Revolutionary SiC3 Coating offers the following advantages
- Cubic structure giving high density coating. This vastly improves corrosion resistance and increases the component’s life.
- Excellent coverage down blind holes. With 30% coating thickness down a Ø1x5mm deep hole.
- High purity coating. Is achievable by using high purity gases in the coating process, while also remaining low in N2 absorption to achieve higher than industry standard purity.
- Adjustable surface roughness. The coating process can be tailored to give different surface roughnesses.
SiC 3 Coating – Silicon Carbide Coated Graphite
Penetration
A huge advantage of SIC3 manufactured by the CVD technology, over line of sight process, is its “throwing power” or penetration depth. Hole diameters down to 1mm can be coated to a depth of 5mm, while still maintaining 30% layer thickness at its deepest point. Even more consistent layer thicknesses can be achieved when larger diameter holes are coated.
Applications
Protective coating for graphite components used in MOCVD, EPI, Semiconductor and LED manufacturing.
SiC3 Ceramic Coating
SiC3, short for cubic silicon carbide, is the isotropic, pure silicon carbide coating offered by CGT Carbon for a wide range of applications. High temperature resistant materials such as graphite, SiC based ceramics and some refractory metals such as tungsten and molybdenum can be coated in SiC3. The coating protects the underlying material against corrosion, oxidation, acts as a diffusion barrier and prevents absorption and desorption of impurities from the underlying material which can interfere with your processes. The coating also prevents particles from the underlying material interfering with the process or device to be made in the process. In combination with porous materials such as graphite, the upper layer of graphite is infiltrated with SiC3 coating, resulting in ultimate adhesion and corrosion protection. Applications can be found in the semi-conductor industry, LED manufacturing, solar, special heat treatment and aerospace.
CGT Carbon Coatings
As an independent graphite and coating supplier, CGT Carbon offers short delivery times, competitive cost and the highest quality standards. The coating produced has a preferential cubic, 3C structure which gives the best corrosion protection when compared to other SiC structures. Not restricted to specific graphite qualities or other material grades we can provide bespoke solutions for bespoke problems.
Technology and general characteristics
CGT Carbon uses CVD technology to manufacture thin SiC3 layers between 10 and 200 µm. The coating produced has a preferential cubic, 3C structure which gives the best corrosion protection when compared to other SiC structures. Standard thickness is 80 – 100 µm and the technology allows to cover all areas with a dense coating. Small, blind holes are coated even for holes with a 1 mm diameter and over 5 mm depth. Products are placed in a reactor on pure materials compatible to the process such as purified graphite and pre-coated SiC3 support materials. Combined with the use of semiconductor grade gases, it leads to a coating with minimum impurity levels and therefore improved corrosion resistance. The design of the reactor ensures only highly pure materials are present in the high temperature zone, along with high purity gases which results in extremely pure layers with a high electrical resistivity. High temperature processes at end customers, have proven the outstanding quality of the SiC3 coating, often outperforming OEM based solutions.
Wafers (silicon, sapphire, SiC, GaN) treated will benefit from the high purity and well defined SiC3 interface. Thermal conductivity is high and thermal transfer is not limited through the coating. Other material properties conform with theoretical values.
At the moment the maximum sized part is restricted to 360mm. In the future CGT Carbon will offer also larger sized parts.
General Properties
The coating can be used in semiconductor, aerospace and heating technologies. It will provide a high purity and impervious layer on graphite, porous ceramics and composites. The combination of graphite selection and graphite machining expertise, offered by CGT Carbon, will ensure that customers experience optimal support for various critical components within these industries. Layer thickness can be varied but typically a layer of 80 – 100µm is achieved.
SiC3 Specification
Listed below are the typical values for some of the important properties for SIC3. Some of these (i.e. crystal size, electrical resistivity) can be customised and optimised for specific applications.
Property | Value |
---|---|
Density | 3200 kg.m-3 |
Crystal Structure | 3C (cubic; β) |
Porosity | 0% (helium leak tight) |
Crystal Size | 1 – 5 µm |
Visual Appearance | Grey, satin to dull |
Thermal Expansion (RT -400oC) | 4.2 x 10-6m.K-1 |
Thermal Conductivity (@20oC) | 200 W.m-1.K-1 |
Elastic Modulus | 450 GPa |
Electrical Resistivity (@20oC) | 1MΩ.m |
XDR
The peaks shown in the diagram perfectly match the 3C crystal structure.

Surface Roughness
The surface roughness parameters are Ra = 0.8µm, Rz = 5µm and Rt = 8µm.
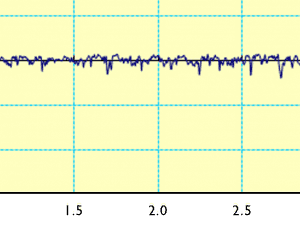
Material Purity
The below table shows the impurities of SiC3 coating
Lowest limit of detection with this method. Testing carried out by EAG Laboratories using Glow Discharge Mass Spectroscopy.
Element | Impurities (PPM) |
---|---|
Sodium | <0.01 |
Magnesium | <0.01 |
Aluminium | <0.02 |
Potasium | <0.5 |
Calcium | <0.05 |
Titanium | <0.005 |
Vanadium | <0.005 |
Chromium | <0.3 |
Iron | <0.04 |
Cobolt | <0.05 |
Nickel | <0.05 |
Molybdenum | <0.05 |
Tin | <0.05 |
Tungsten | <0.01 |