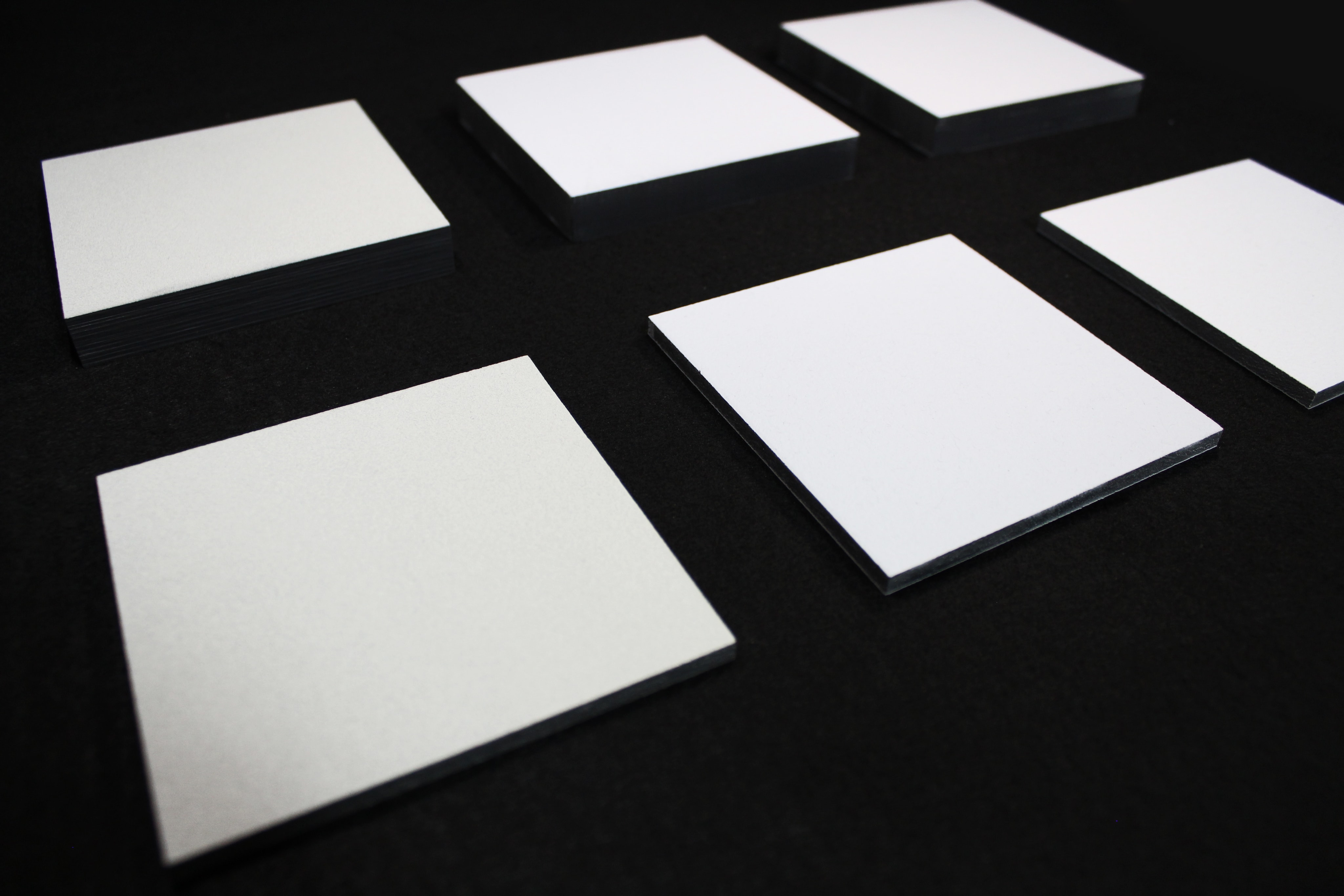
Plasma Spray Coating
Plasma spray coating is a coating method based on the generation of a stream of very hot ionized plasma gas. The coating material is injected into the plasma gas stream, typically in the form of a powder mixed with an inert gas. The plasma gas flow with a temperature of over 12000 K and a velocity of 400 - 800 m/s is the source of heat and velocity required to melt and propel the coating material to the part surface. The coating material solidifies on the part surface and creates a coherent coating layer.
The main advantages
- Highly versatile coating method that allows coating with many different compounds to achieve different surface properties.
- The high temperature of the plasma gas jet allows the use of materials with a high melting point for the coating and thus the achievement of a high temperature resistance of the coated surface.
- Increase of durability, hardness and wear resistance of the coated surface.
- Thermal and electrical insulation, improved thermal shock resistance of the coated surface.
- Better performance and lower maintenance costs, resulting in a longer service life.
Alumina (Al2O3)
Alumina is the most commonly used oxide of aluminium with wide industrial use. Coating with alumina is very wear resistant, chemically inert and stable at medium temperatures, depending on the crystalline phase and deposition temperature. Other advantages are the elimination of arcing, very good non-stick properties of the coated surface and the inert layer acts as a separating layer between graphite and metal parts and prevents carburisation.
Zirconium dioxide (ZrO2)
Zirconia is a white crystalline oxide of zirconium. Zirconium oxide coatings are usually stabilized with other elements such as yttrium (in the form of yttria (Y203)) to further improve its properties.