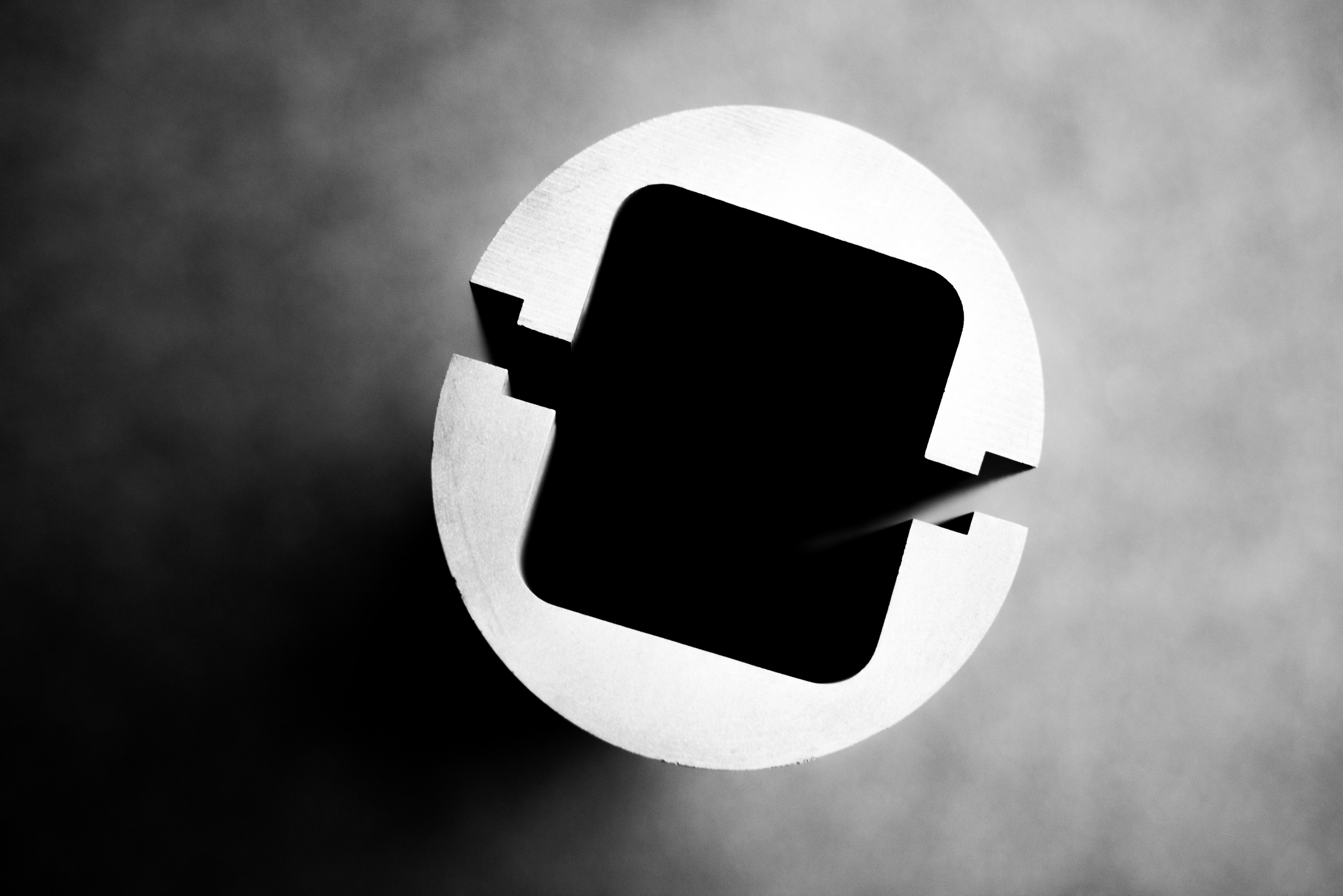
Прессованный Графит (Серия CGM)
Прессованные графиты с мелким размером зерна обладают высокой анизотропией. Этот материал обеспечивает чрезвычайно широкий спектр свойств с точки зрения механической прочности, трения и проводимости, которые можно дополнительно улучшить путем пропитки смолами или металлами.
Благодаря своей мелкозернистой и однородной структуре графиты CGM часто могут заменить более дорогие графиты изостатического прессования. Однако их размеры ограничены.
Процесс производства прессованного графита
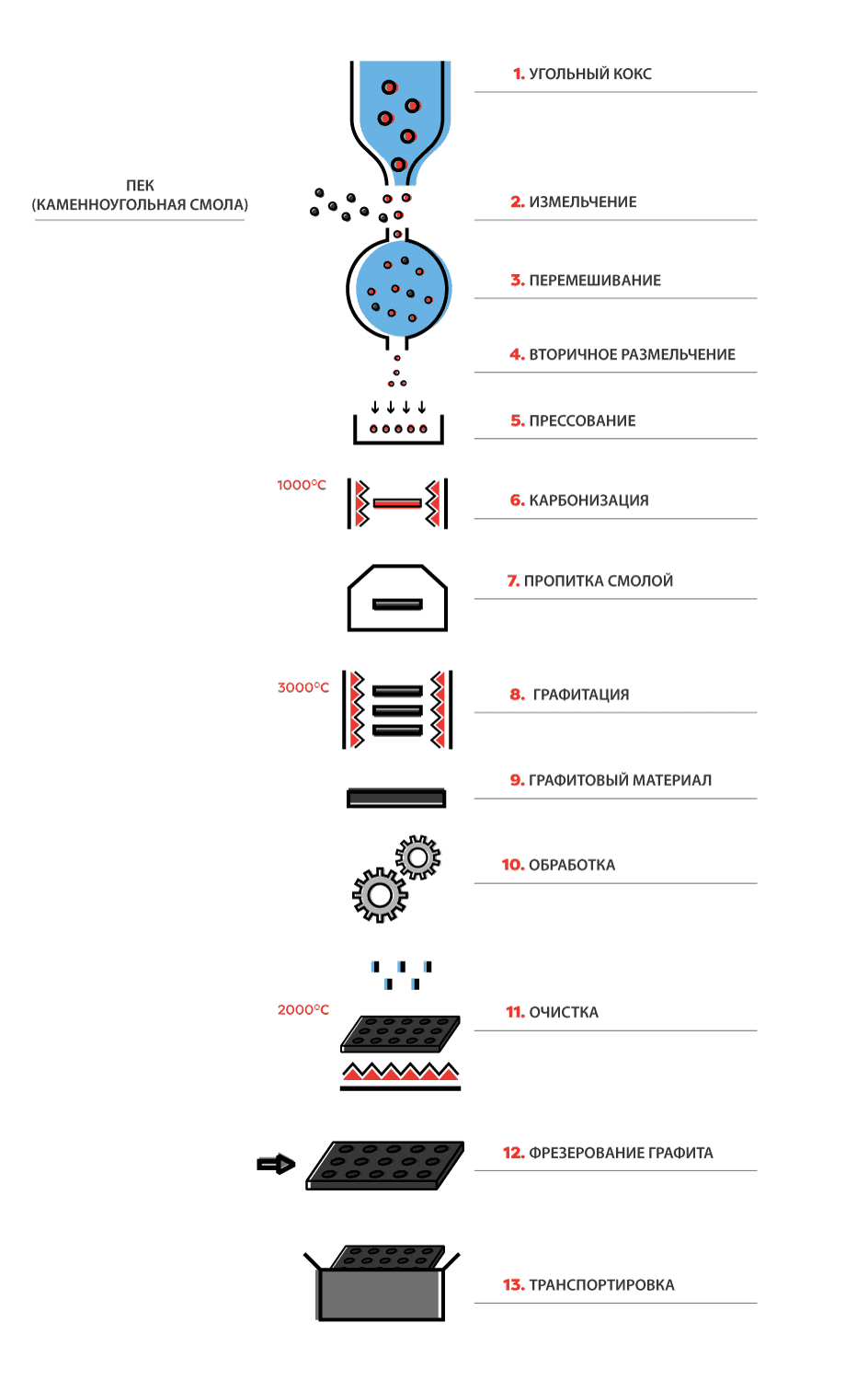
1. УГОЛЬНЫЙ КОКС
Угольный кокс — ингредиент, получаемый на коксохимических заводах путем нагревания каменного угля (600—1200 °С). Этот процесс происходит в специально сконструированных коксовых печах с использованием дымовых газов и ограниченного доступа кислорода. Отличается более высокой теплотворной способностью(теплотой сгорания), чем обычный уголь.
2. ИЗМЕЛЬЧЕНИЕ
После проверки сырья, его измельчают до определенного размера зерна. Дробильные машины сортируют очень мелкую угольную пыль в мешки в зависимости от размера зерна.
ПЕК (КАМЕННОУГОЛЬНАЯ СМОЛА)
Пек представляет собой густую черную жидкость. Это побочный продукт коксования каменного угля без доступа воздуха при температуре 1000-1200°С.
3. ПЕРЕМЕШИВАНИЕ
Когда процесс помола кокса завершен, его смешивают с пеком. Оба компонента смешивают при высокой температуре, чтобы расплавить пек и смешать его с коксовыми зернами.
4. ВТОРИЧНОЕ РАЗМЕЛЬЧЕНИЕ
После процесса смешивания образуются маленькие углеродные шарики, которые необходимо размельчить в пыль.
5. ПРЕССОВАНИЕ
Прессование — это метод уплотнения порошка путем прикладывания одноосного давления на порошок, когда он помещен в форму. Давление прикладывается к порошковой смеси в одном направлении и определяется формой пресс-формы, удерживающей давление. Прикладывая различное давление на пресс-форму, можно получить различные свойствах графита.
6. КАРБОНИЗАЦИЯ
Следующий и самый продолжительный этап (2-3 месяца) – карбонизация(обжиг) в печи. Равномерно спрессованный материал помещают в большие печи с температурой до 1000°С. Чтобы не было дефектов и трещин, температура в печи постоянно контролируется. Когда обжиг завершен, блок приобретает желаемую твердость.
7. ПРОПИТКА СМОЛОЙ
На этой стадии процесса блок может быть пропитан смолой и повторно обожжен для уменьшения его пористости. Пропитку обычно проводят смолой с меньшей вязкостью, чем у смолы(пека), используемого в качестве связующего. Низкая вязкость смолы необходима для лучшего заполнения пор.
8. ГРАФИТАЦИЯ
На этом этапе матрица атомов углерода уже упорядочена и процесс перехода от углерода к графиту называется графитацией. Графитация – это нагрев полученных блоков до температуры около 3000°С. После графитации плотность, электропроводность, теплопроводность и коррозионная стойкость значительно улучшаются, также повышается эффективность обработки.
9. ГРАФИТОВЫЙ МАТЕРИАЛ
После графитации необходимо проверить все свойства графита, включая размер зерна, плотность, прочность на изгиб и сжатие.
10. ОБРАБОТКА
После того, как материал полностью подготовлен и проверен, его можно использовать в производстве согласно технической документации заказчика.
11. ОЧИСТКА
Если изостатический графит используется в производстве полупроводников, монокристаллов кремния и в атомной энергетике, требуется его высокая чистота, поэтому все примеси должны быть удалены химическими методами. Общепринятой практикой удаления загрязнений из графита является помещение графитированного продукта в газообразный галоген и нагрев его до температуры около 2000°С.
12. ФРЕЗЕРОВАНИЕ ГРАФИТА
В зависимости от области применения, графит может быть обработан и иметь гладкую поверхность.
13. ТРАНСПОРТИРОВКА
После конечной обработки вырезанный материал или готовая графитовая деталь тщательно упаковываются и отправляются заказчику.
Наш графит CGM может поставляться в виде блоков и кругов различных размеров и может быть очищен до <5 ppm по запросу клиента. Мы можем помочь вам выбрать необходимый тип графита - просто свяжитесь с нами.